Noel Finn marked 40 years at Baker Labels last year – having joined the company in 1979 when Baker Labels was still based in Vale Royal in Kings Cross. With the exception of our Managing Director Steve Baker, Noel is our longest standing member of staff so we’d like to give you a little insight into how he ticks.
Name: Noel Finn
Position: Quality Control
At Bakers since: 1979
The business is almost unrecognisable now compared to back then. Noel remembers how you could be multi coloured by the time you left work and you had to wash you hands in paint thinners every day.
“Everything was done by hand back then. It was much slower but there was more skill involved – you had to be aware of so much and people would come in the door and show you a bit of wood or something and say “can you match that colour?” and I would mix the colours, have a few tricks and do the colour match. Colours are easier now because everyone uses pantone books to choose colours from.”
Noel’s first role was operating a Gestetner litho machine but he learned to operate various presses over the years. Always one to be busy, if there was no work on the press he was operating he’d look for work elsewhere in the factory – helping where he was needed, even if that was painting the walls or cutting and creasing paper on the massive old Heidelberg.
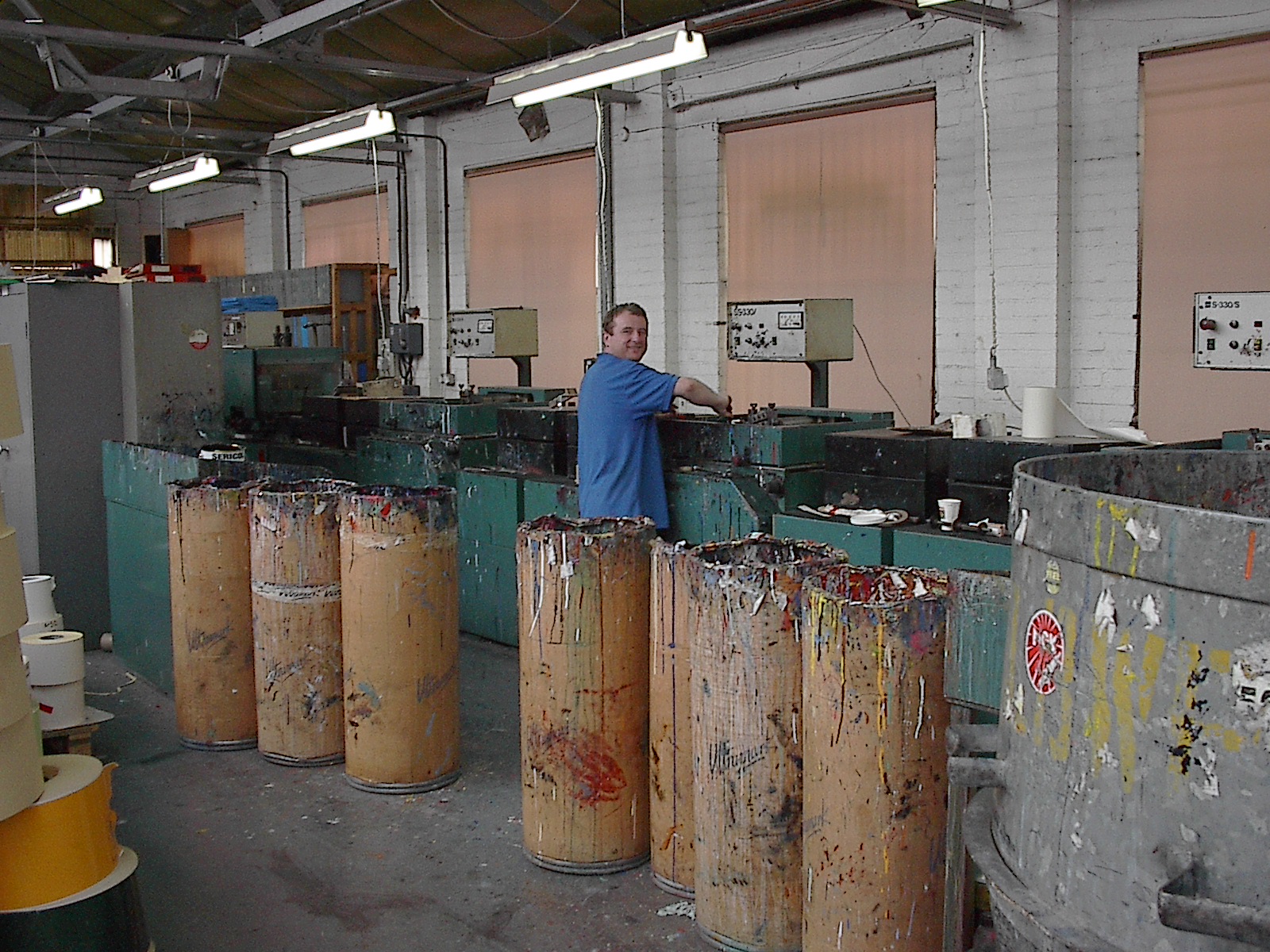
“Roy was strict but fair. You all worked, no skivers. You’d get it right or you’d get out.”
When Roy Baker bought the company’s first Nilpeter S330-S Noel was entrusted with the job to run it.
“With the Nilpeter, from start to finish I was in control of the whole process. From ordering the material to the moment it was ready to go out the door. It had a hot foil unit, four screen printing heads, a die cutter and even an inline guillotine built by a friend of Roy’s”
At over 20m long it meant Noel covered a lot of distance over the course of the day and it wasn’t without its challenges.
“It was murder to keep in register because you were putting a rotary material through a flatbed machine – you had to watch it all the time. Even now I’ll say to the operators, “If you think your press is running alright, then it isn’t. You have to keep your eye on the press all the time.”
Noel ran that Nilpeter for years and as both printer and finisher of every job on the press, he took a great deal of pride in his work.
“What I did on that press paid for the next machine. I’m proud of that.”
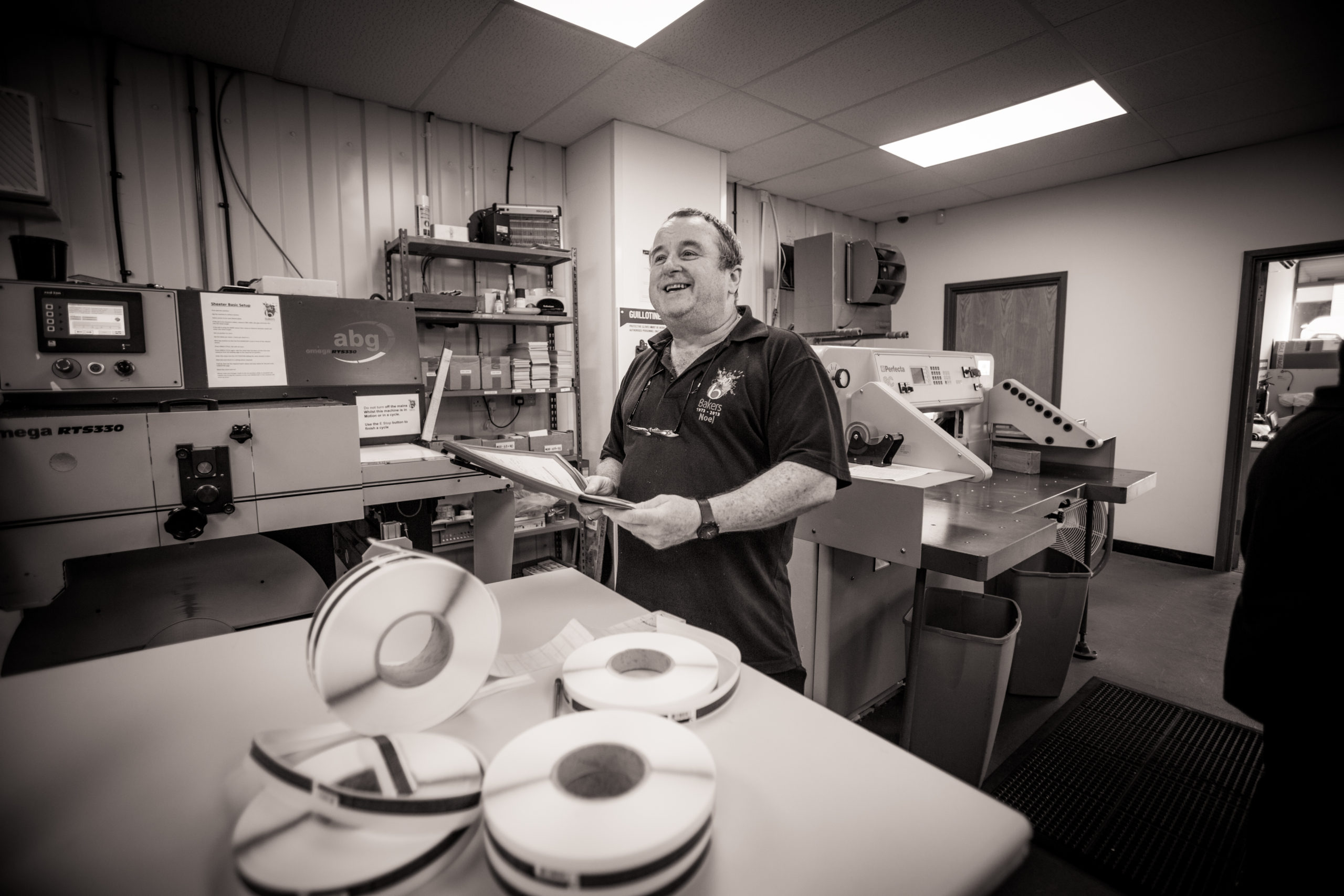
Having been at Bakers since the very early days, Noel can remember Roy Baker initially only ever buying second hand machines and how they would make things work to get the jobs done, even holding things together with elastic bands – a far cry from the state of the art factory we see today.
Decades ago, health and safety would be seen more as a hinderance. The phrase “The safety cut-outs get in the way” was a common phrase, and it wasn’t unusual for minor accidents to happen if you weren’t paying attention. Blood, sweat and tears were expected to get the jobs done!
It’s a very different story these days with strict safety and maintenance measures as standard practice in all departments at Bakers.
What does Noel think has made the company so successful?
“It’s got to be the work, the finished product. We’re good at it. Plus the continual reinvestment of new equipment, with one machine paying for the next means we’re spoiled for equipment now. We produce thousands of labels every day and our customers rely on a very high level from us because 90% of our customers are trade.”
Typical day for Noel

Start at 6am. The majority of staff start at 8.30am at Bakers so it’s quiet when Noel arrives and starts checking the work that’s been completed and is due to be shipped out the door that morning.
“I look out for mistakes before anything goes out the door. Knowing what it should look like before it goes takes a long time to learn, especially nowadays when everything comes through the computer. There’s a frustration for me that you can’t feel and touch it or change it.
We produce so many labels every day that there will always be mistakes and it’s our job in QC to stop it going out the door. We don’t want the customers receiving anything wrong so we reproduce the jobs again. I’d rather a customer rings up to say there are two labels missing (where I’ve removed two to test them) than send back a whole reel because they’re wrong.
It’s very frustrating if I miss something and for me, colours are the worst things to get wrong.”
Noel has a lot of experience and knowledge to share with new, younger members of staff.
I’m always asking questions. You can never ask enough questions and I know the way I say things isn’t taken well sometimes. I don’t mince my words. You can’t pussy foot around. We need to get the work done you’ve got to nip things in the bud. It’s production at the end of the day and jobs have got to get out the door.
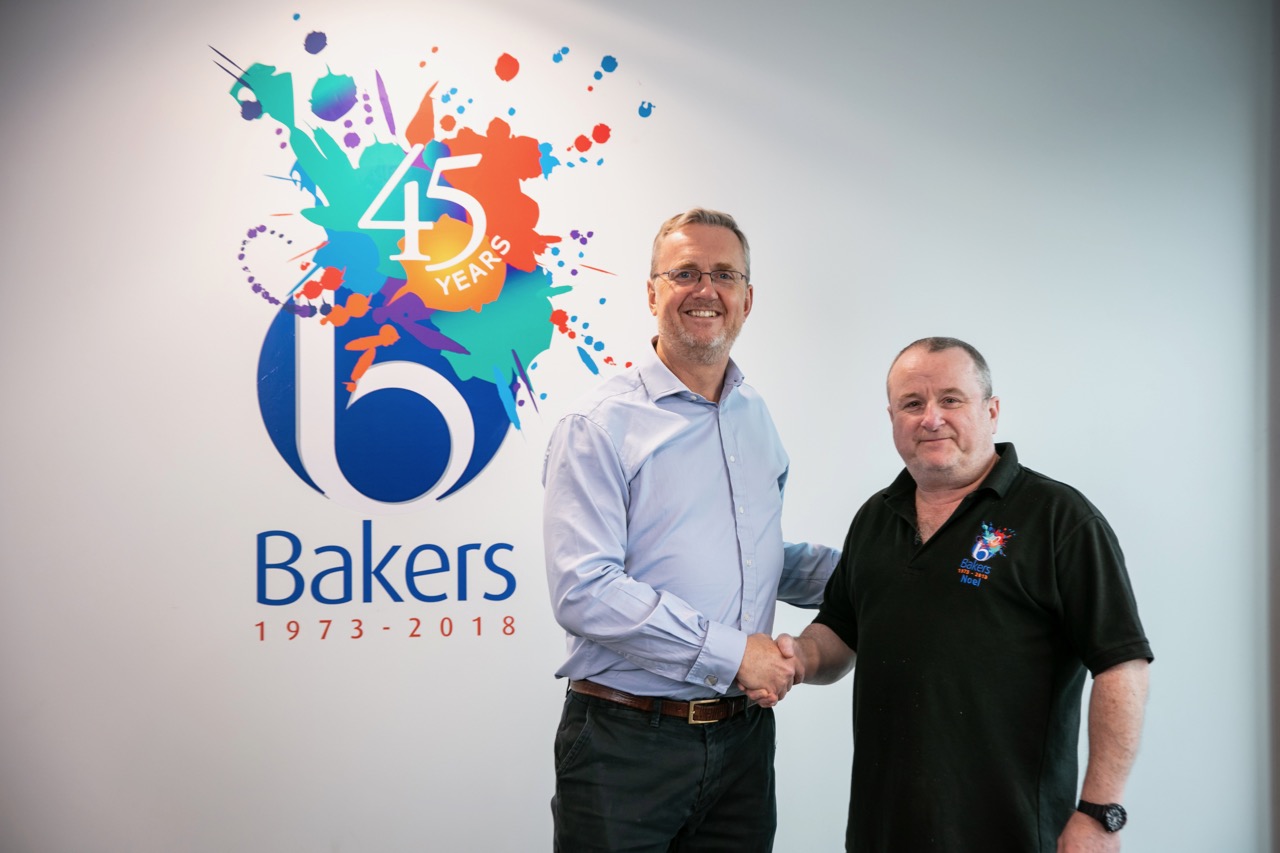